Introduction: Certified Welding Inspector
Welding, the art of fusing materials together using heat and pressure, stands as a cornerstone of modern industrialization. From towering skyscrapers to intricate machinery, welding underpins the structures and equipment that propel our world forward. Yet, within this intricate dance of metal and flame, there exists a critical need for precision and adherence to standards to ensure both quality and safety.
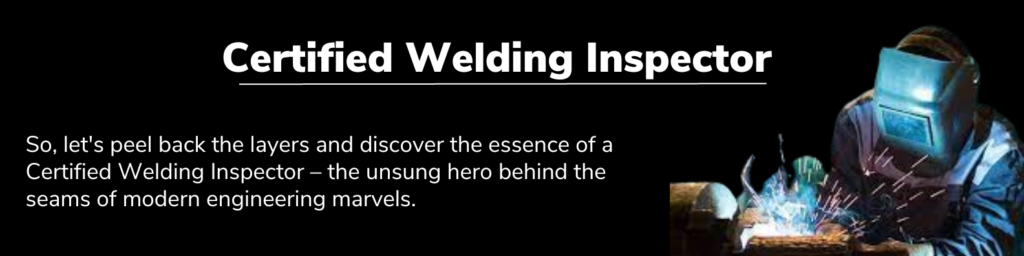
Enter the Certified Welding Inspector (CWI), a sentinel of excellence in the welding realm. As industries continue to push the boundaries of innovation, the role of a CWI emerges as a linchpin in maintaining weld integrity and upholding stringent regulations. This blog embarks on a journey into the heart of this vocation, shedding light on the multifaceted responsibilities, rigorous qualifications, and far-reaching impact of Certified Welding Inspectors.
In the following sections, we will delve into the intricate world of these inspectors, who possess the trained eye and expertise to discern between a sound, durable weld and a potential point of failure. From the heat of the welding torch to the depths of technical codes, we will uncover the pivotal role CWIs play in guaranteeing weld quality, enforcing safety measures, and consequently, elevating standards across various industries.
So, let’s peel back the layers and discover the essence of a Certified Welding Inspector – the unsung hero behind the seams of modern engineering marvels.
Understanding the Certified Welding Inspector Role
At the heart of every successful welding endeavor stands the vigilant figure of the Certified Welding Inspector (CWI). Tasked with a pivotal responsibility, the CWI is entrusted with the critical role of meticulously inspecting and guaranteeing the quality of welded materials and structures. This role isn’t just about scrutinizing the outward appearance of welds; it’s about safeguarding the integrity of the final product and the safety of all who encounter it.
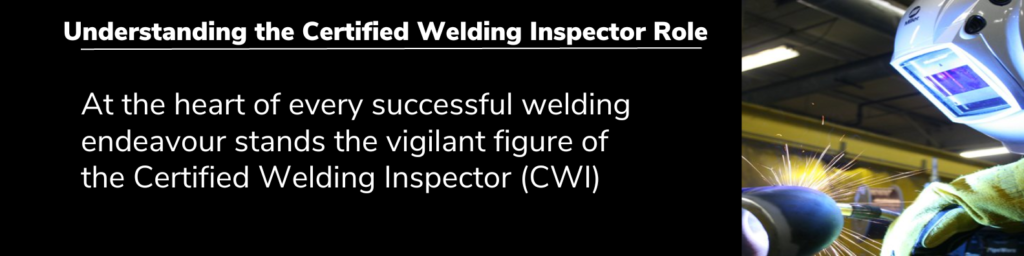
Importance in Preventing Defects and Ensuring Safety
In the realm of welding, the stakes are high – a minor flaw in a weld can escalate into a catastrophic failure, causing injury, financial losses, and reputational damage. This is where the CWI’s expertise shines through. By adhering to a stringent code of quality, CWIs play a pivotal role in identifying and mitigating potential defects in welds. Whether it’s subtle imperfections like porosity or more pronounced issues like inadequate fusion, a CWI’s trained eye is calibrated to spot even the slightest deviations from the norm.
Beyond mere mechanics, the role of a CWI extends to ensuring safety. Welds are not only integral to the structural integrity of buildings, bridges, and machinery but also to the safety of those who use them. A subpar weld, compromised by defects, might fail under duress, leading to catastrophic consequences. By upholding industry standards and meticulously evaluating weld quality, CWIs act as the first line of defense against potential hazards, thereby contributing significantly to overall safety.
Maintaining Industry Standards
In an ever-evolving industrial landscape, adhering to standardized practices is paramount. CWIs act as the custodians of these standards, ensuring that welds are not only safe but also comply with the latest codes and regulations set by organizations such as the American Welding Society (AWS) and various international bodies. Their meticulous inspections and verifications form a vital link in the chain of quality control, fostering consistency and reliability in welded structures across diverse industries.
In essence, the role of a Certified Welding Inspector is a guardian of quality and safety. It’s a role that extends beyond the weld bead and delves deep into the core of industrial craftsmanship, where precision and vigilance combine to shape a world where welded structures stand strong and secure.
Qualifications and Certification
The most recognized welding inspector certification is the Certified Welding Inspector (CWI) certification, which is offered by the American Welding Society (AWS). To become a CWI, you must have a high school diploma or equivalent, at least two years of welding experience, and pass a written and practical exam.
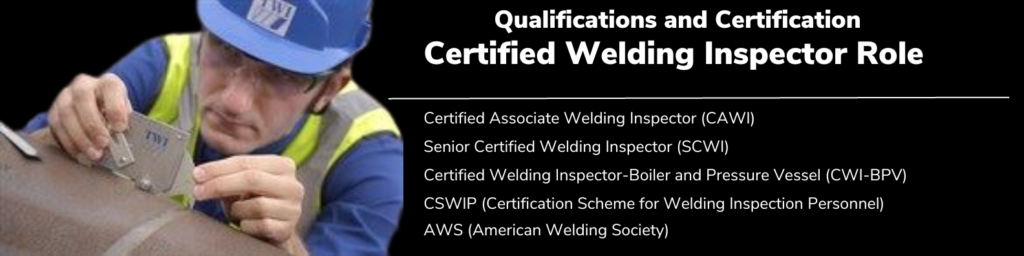
There are also other welding inspector certifications available, such as:
- Certified Associate Welding Inspector (CAWI): This is a lower-level certification that is designed for individuals who are new to welding inspection.
- Senior Certified Welding Inspector (SCWI): This is a higher-level certification that is designed for individuals who have more experience in welding inspection.
- Certified Welding Inspector-Pipeline (CWI-P): This certification is designed for individuals who inspect pipelines.
- Certified Welding Inspector-Boiler and Pressure Vessel (CWI-BPV): This certification is designed for individuals who inspect boilers and pressure vessels.
- CSWIP (Certification Scheme for Welding Inspection Personnel) and AWS (American Welding Society) are both organizations that offer welding inspector certifications. CSWIP is a UK-based organization, while AWS is a US-based organization.
- The CSWIP welding inspector certification is more widely recognized in Europe, while the AWS welding inspector certification is more widely recognized in North America. However, both certifications are respected and recognized internationally.
- The specific requirements for the CSWIP and AWS welding inspector certifications are similar. However, there are some differences in the content of the exams. The CSWIP exam focuses more on the theoretical aspects of welding inspection, while the AWS exam focuses more on the practical aspects of welding inspection.
- Ultimately, the best welding inspector certification for you will depend on your individual circumstances and goals. If you are located in Europe or want to work in Europe, then the CSWIP certification may be a better choice for you. If you are located in North America or want to work in North America, then the AWS certification may be a better choice for you.
The specific certification requirements vary depending on the organization that offers the certification. However, all of the certifications require a certain level of education, experience, and knowledge in welding inspection.
In addition to certification, welding inspectors may also need to have other skills, such as:
- Excellent communication skills
- The ability to work independently and as part of a team
- The ability to read and interpret technical drawings
- The ability to use welding inspection equipment
If you are interested in becoming a welding inspector, I recommend that you research the different certification programs available and choose one that is right for you. You should also gain as much welding experience as possible before you take the certification exam.
CSWIP (Certification Scheme for Welding Inspection Personnel) and AWS (American Welding Society) are both organizations that offer welding inspector certifications. CSWIP is a UK-based organization, while AWS is a US-based organization.
The CSWIP welding inspector certification is more widely recognized in Europe, while the AWS welding inspector certification is more widely recognized in North America. However, both certifications are respected and recognized internationally.
The specific requirements for the CSWIP and AWS welding inspector certifications are similar. However, there are some differences in the content of the exams. The CSWIP exam focuses more on the theoretical aspects of welding inspection, while the AWS exam focuses more on the practical aspects of welding inspection.
Ultimately, the best welding inspector certification for you will depend on your individual circumstances and goals. If you are located in Europe or want to work in Europe, then the CSWIP certification may be a better choice for you. If you are located in North America or want to work in North America, then the AWS certification may be a better choice for you.
Here is a table comparing the CSWIP and AWS welding inspector certifications:
Specification | CSWIP | AWS |
---|---|---|
Organization | Certification Scheme for Welding Inspection Personnel (UK) | American Welding Society (US) |
Scope | International | International |
Focus | Theoretical | Practical |
Recognition | Widely recognized in Europe | Widely recognized in North America |
Requirements | High school diploma or equivalent, at least two years of welding experience, and pass a written and practical exam | High school diploma or equivalent, at least two years of welding experience, and pass a written and practical exam |
Cost | Varies depending on the level of certification | Varies depending on the level of certification |
Key Responsibilities of a Certified Welding Inspector
A Certified Welding Inspector (CWI) wears many hats, each crucial to upholding weld quality and safety. Let’s explore the primary responsibilities that define their role.
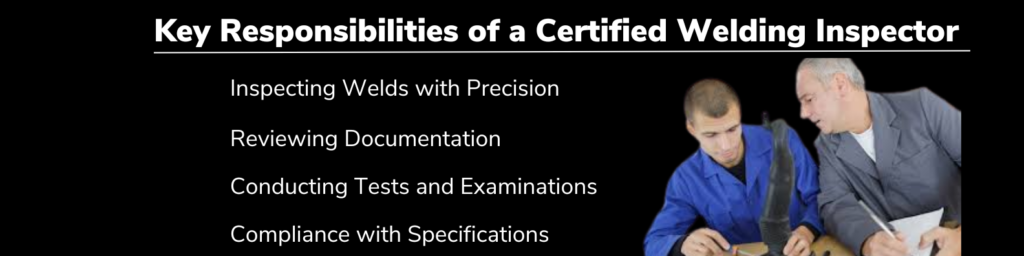
1. Inspecting Welds with Precision
At the heart of a CWI’s duties is the meticulous inspection of welds. CWIs employ their trained eye to scrutinize weld joints for defects, ensuring they adhere to industry standards and codes. From identifying cracks, porosity, and improper fusion to assessing weld bead profiles, a CWI’s expertise guarantees that every weld meets the stringent requirements set forth.
2. Reviewing Documentation
Beyond the visible welds, a CWI delves into the realm of paperwork. They review welding procedures, certifications, and other documentation to ensure that the welding process aligns with approved methods. This step ensures that the entire welding process, from the materials used to the welding techniques applied, is in accordance with industry standards.
3. Conducting Tests and Examinations
A CWI is equipped to go beyond visual inspections. They may carry out non-destructive testing (NDT) methods such as radiographic testing, ultrasonic testing, and magnetic particle testing. These tests uncover hidden defects that might not be visible to the naked eye, contributing to a comprehensive assessment of weld integrity.
Collaboration for Compliance
The role of a CWI extends beyond the inspection booth, encompassing collaboration with various stakeholders:
1. Welding Personnel: CWIs collaborate closely with welders, offering guidance and feedback on weld quality. They serve as mentors, helping welders understand and rectify issues while adhering to industry best practices.
2. Engineers: Engineers rely on CWIs to ensure that their design specifications are met on the shop floor. This collaboration helps bridge the gap between theoretical design and practical execution, contributing to the creation of safe and functional structures.
3. Project Managers: CWIs serve as a checkpoint in project management, ensuring that welds are completed correctly and on schedule. Their insights help prevent delays caused by rework or non-compliance with standards.
4. Compliance with Specifications
CWIs act as intermediaries between engineering specifications and real-world welding. They interpret and apply technical codes and standards, translating them into tangible guidelines for welders to follow. By doing so, they ensure that the end product not only meets design intent but also surpasses expectations in terms of safety and quality.
Importance in Welding Quality Assurance
In the intricate world of welding, where the strength of a connection can determine the reliability of a structure, Certified Welding Inspectors (CWIs) emerge as guardians of quality assurance. Their role is nothing short of instrumental in maintaining weld integrity, consistency, and the overall success of projects. Let’s delve into the critical aspects of their contribution.
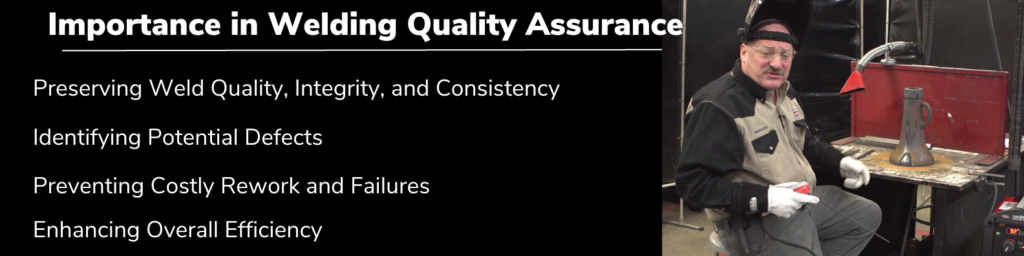
Preserving Weld Quality, Integrity, and Consistency
Weld quality isn’t a mere afterthought; it’s the foundation upon which the entire structure stands. CWIs stand as sentinels, ensuring that every weld meets the stringent standards necessary for longevity and safety. By meticulously examining welds, they verify the integrity of the joint and the uniformity of the fusion. Their expertise prevents defects that might compromise the structural strength, minimizing the risk of catastrophic failures in the future.
Identifying Potential Defects
A CWI’s trained eye extends beyond the surface, penetrating into the intricacies of welds to identify potential defects that might escape the untrained observer. These defects, if unchecked, can range from minuscule cracks to hidden porosity, or even improper weld penetration. By spotting these imperfections, CWIs prevent the flaws from magnifying into substantial issues that might jeopardize the structure’s safety or lead to costly rework.
Preventing Costly Rework and Failures
Imagine the consequences of a poorly executed weld going unnoticed—compromised structural integrity, expensive repairs, and potential legal liabilities. This is where CWIs shine brightest. By identifying defects at the earliest stages, they prevent these issues from snowballing into larger, more expensive problems down the line. This proactive approach saves not only resources but also the reputation of projects and the safety of individuals who rely on them.
Enhancing Overall Efficiency
The presence of CWIs isn’t merely about spotting defects. Their involvement streamlines the welding process by ensuring compliance with codes and standards from the outset. By providing real-time feedback to welding personnel, CWIs contribute to a culture of quality and continuous improvement. This results in fewer rejections, reduced rework, and overall cost savings for projects.
Ensuring Safety and Compliance: Certified Welding Inspector
In the realm of welding, where strength and reliability are paramount, the role of a Certified Welding Inspector (CWI) extends far beyond surface aesthetics. CWIs are the unsung heroes of safety, meticulously ensuring that every weld adheres to industry codes and safety regulations. Their dedication to upholding these standards is a linchpin in the foundation of secure structures and safe environments.
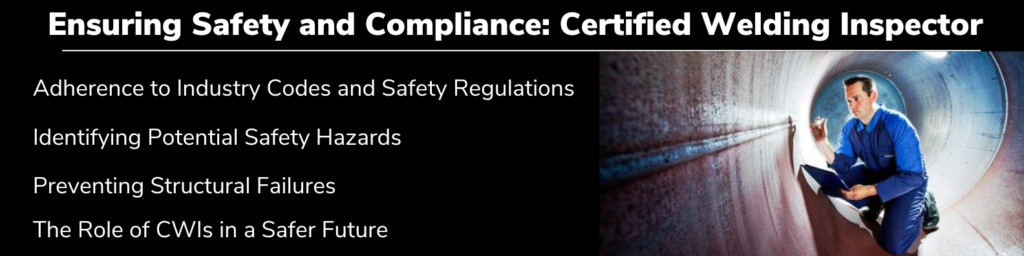
Adherence to Industry Codes and Safety Regulations
Industry codes and safety regulations are the backbone of welding practices. CWIs serve as staunch enforcers of these guidelines, validating that each weld aligns with established norms. This ensures that structures, whether they’re towering skyscrapers or vital infrastructure, possess the structural integrity necessary to withstand the rigors of time and usage.
Identifying Potential Safety Hazards
Welding, though transformative, carries inherent risks. CWIs, armed with extensive knowledge and practical experience, are adept at recognizing potential safety hazards. They scrutinize welds not only for visual imperfections but also for structural vulnerabilities that might compromise the safety of the entire structure. By identifying weak points early on, CWIs prevent potential accidents or failures that could lead to harm or financial losses.
Preventing Structural Failures
A single faulty weld, left unchecked, can have far-reaching consequences. The collapse of a bridge, the malfunction of machinery, or the rupture of a pipeline are all possible outcomes of subpar welding practices. CWIs act as proactive defenders against such scenarios. By detecting flaws in welds—such as cracks, incomplete fusion, or improper penetration—they mitigate the risks of structural failures that could have dire consequences.
The Role of CWIs in a Safer Future
The role of a CWI goes beyond the immediate project. Their dedication to safety sets a precedent for an industry committed to uncompromising quality. With each weld they inspect and approve, they contribute to a safer, more secure future where structures withstand the test of time and environments foster well-being.
Impact on Industry and Projects: Certified Welding Inspector
Certified Welding Inspectors (CWIs) are the unsung heroes behind the scenes, wielding a profound impact on industries ranging from construction to manufacturing and infrastructure development. Their expertise ripples through projects, leaving a trail of enhanced quality, reduced costs, and improved outcomes.
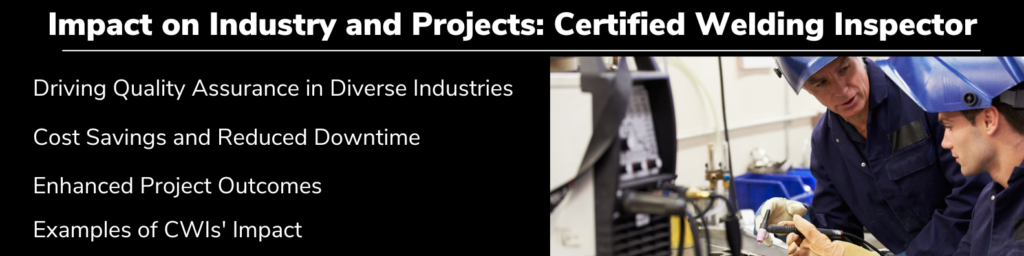
Driving Quality Assurance in Diverse Industries
In construction, the integrity of buildings and bridges hinges on the precision of welds. CWIs ensure that welds are not only strong but also free from defects that could compromise structural stability. In manufacturing, whether it’s automotive, aerospace, or machinery production, CWIs guarantee the reliability of welded components, safeguarding against failures that could lead to recalls or accidents. Even in the expansive realm of infrastructure development, from pipelines to power plants, CWIs’ presence guarantees weld integrity and operational safety.
Cost Savings and Reduced Downtime
A single welding defect can have costly consequences. A flawed weld in a critical support beam might necessitate expensive repairs or replacements. In manufacturing, a defective weld might lead to production delays and disruptions. CWIs’ vigilance prevents such pitfalls. Their early detection of issues means that defects are rectified before they escalate into expensive problems, saving substantial costs and minimizing downtime.
Enhanced Project Outcomes
Imagine a construction project completed on time, a manufacturing line running smoothly, or an infrastructure development without unforeseen setbacks. CWIs contribute to these success stories. By ensuring that welds adhere to standards and codes, they foster a culture of quality that translates into the seamless execution of projects. Confidence in the integrity of welds elevates the overall reliability of structures and components.
Examples of CWIs’ Impact
- In the construction of a suspension bridge, a CWI’s meticulous inspections ensure that every weld connecting the intricate framework is defect-free. This diligence prevents potential bridge failures, ensuring the safety of commuters.
- In a manufacturing plant, a CWI identifies a minor defect in a key component of an industrial machine. Rectifying the issue prevents a potential breakdown, saving the manufacturer significant downtime and maintenance costs.
- During the development of a pipeline for transporting hazardous materials, a CWI’s expertise guarantees weld quality and adherence to safety standards. This diligence averts potential environmental disasters and costly legal liabilities.
Challenges Faced by Certified Welding Inspector
The role of a Certified Welding Inspector (CWI) is one of vigilance, precision, and responsibility. However, this role doesn’t come without its share of challenges. CWIs navigate a complex landscape where the pursuit of quality assurance intersects with various project demands and stakeholder considerations. Let’s explore some of the challenges they might encounter.
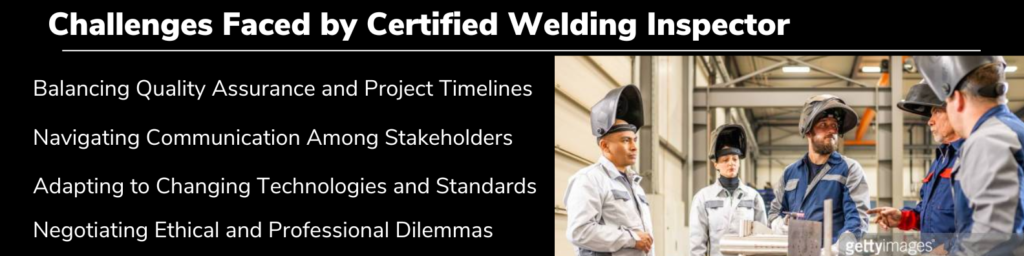
Balancing Quality Assurance and Project Timelines
In industries where time is often of the essence, CWIs find themselves in a delicate balancing act. While their primary focus is on ensuring weld quality and safety, they also must align with project timelines. Striking the right balance between thorough inspections and timely progress can be challenging. The pressure to maintain a project’s pace might at times conflict with the meticulous scrutiny required to identify potential defects.
Navigating Communication Among Stakeholders
CWIs are central figures in a multidisciplinary environment. They interact with welding personnel, engineers, project managers, and sometimes even clients. Effective communication is critical for the success of projects, but it can also be a challenge. Translating technical jargon into understandable terms for stakeholders who might not be well-versed in welding intricacies requires finesse. Miscommunication can lead to misunderstandings, delays, or even compromises in weld quality.
Adapting to Changing Technologies and Standards
The world of welding is ever-evolving. New materials, techniques, and codes emerge, shaping the landscape of the industry. For CWIs, staying updated on these advancements is crucial. However, adapting to new technologies and standards while maintaining a consistent level of expertise can be demanding. Continuous learning is a necessity, and this pursuit of knowledge requires dedication and time investment.
Negotiating Ethical and Professional Dilemmas
CWI ethics encompass impartiality, integrity, and a commitment to standards. However, there might be instances where these values clash with real-world scenarios. For instance, CWIs might face pressure to overlook minor defects to meet project deadlines or maintain relationships. Striking a balance between professional standards and external pressures can be a moral dilemma that CWIs must navigate with integrity.
Future Trends and Advancements: Certified Welding Inspector
In the world of welding, the only constant is change. As technology advances and industries evolve, the landscape of welding is undergoing a transformation. This evolution isn’t just limited to machines and materials—it extends to the very role of Certified Welding Inspectors (CWIs). Let’s explore how CWIs are adapting to emerging trends and innovations.
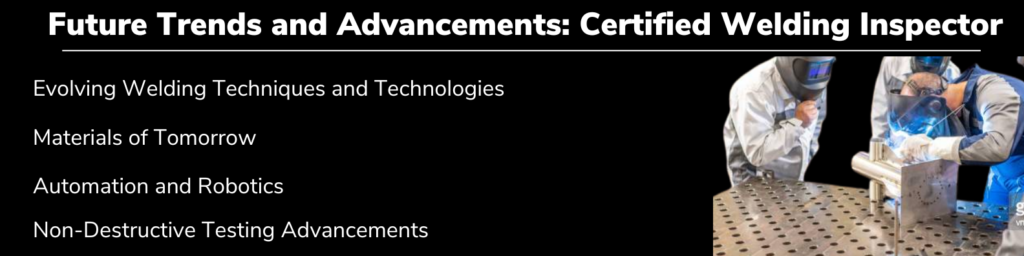
Evolving Welding Techniques and Technologies
New welding techniques are reshaping the way structures are fabricated. From laser welding to friction stir welding, these innovative methods offer advantages in terms of precision, efficiency, and reduced heat-affected zones. CWIs must stay informed about these advancements to ensure they’re inspecting welds using the latest techniques.
Materials of Tomorrow
Materials science is opening doors to a wide array of advanced materials, from high-strength alloys to composite materials. These materials offer improved properties but also present unique challenges in terms of welding. CWIs must be well-versed in the characteristics of these materials and the specific welding procedures required to ensure weld quality.
Automation and Robotics
Automation and robotics are becoming increasingly prevalent in welding processes. While these technologies enhance productivity and consistency, they also introduce a new dimension of inspection challenges. CWIs need to adapt to inspecting welds created by automated systems, and understand how these processes impact weld quality.
Non-Destructive Testing Advancements
Non-destructive testing (NDT) methods are advancing rapidly. Technologies like digital radiography, phased array ultrasonics, and advanced imaging techniques offer greater precision in defect detection. CWIs should be knowledgeable about these NDT methods to choose the most effective one for different scenarios.
Data-Driven Insights
The rise of the Industrial Internet of Things (IIoT) is transforming industries through data collection and analysis. CWIs can leverage this data to gain insights into welding processes and quality trends. This data-driven approach enhances their ability to make informed decisions and detect issues before they escalate.
Continual Learning and Adaptation
As the welding landscape evolves, so must the CWIs. Staying relevant in this dynamic field requires a commitment to continuous learning. CWIs must invest in professional development, attend workshops, and engage with industry experts to remain at the forefront of emerging trends.
Key Role play by Certified Welding Inspector in Oil and Gas Industry
Certified Welding Inspectors (CWIs) play a critical role in the oil and gas industry by ensuring the quality and safety of welded joints. They do this by inspecting welds during fabrication, installation, and maintenance to ensure that they meet all applicable codes and standards.
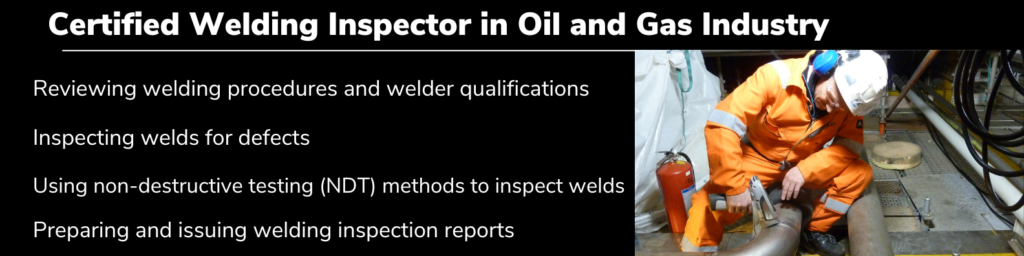
CWIs in the oil and gas industry typically have a wide range of responsibilities, including:
- Reviewing welding procedures and welder qualifications
- Inspecting welds for defects
- Using non-destructive testing (NDT) methods to inspect welds
- Preparing and issuing welding inspection reports
- Training welders and other personnel on welding inspection
- Developing and implementing welding quality assurance programs
CWIs must have a strong understanding of welding principles and practices, as well as the ability to read and interpret technical drawings. They must also be able to work independently and as part of a team, and be able to communicate effectively with engineers, welders, and other stakeholders.
The oil and gas industry is a highly regulated industry, and CWIs play an important role in ensuring that welded joints meet all applicable codes and standards. By doing so, they help to prevent accidents and ensure the safety of workers and the public.
Here are some specific examples of the role that CWIs play in the oil and gas industry:
- They inspect welds on oil and gas pipelines to ensure that they are strong and leak-free.
- They inspect welds on oil and gas well casings to ensure that they are able to withstand the pressure of the fluids underground.
- They inspect welds on oil and gas production equipment to ensure that they are safe and reliable.
- They inspect welds on oil and gas drilling rigs to ensure that they are able to withstand the forces of drilling.
CWIs play a vital role in the oil and gas industry by ensuring the quality and safety of welded joints. Their work helps to prevent accidents and protect workers and the public.
Key responsibilities of Underwater welding by a Certified Welding Inspector
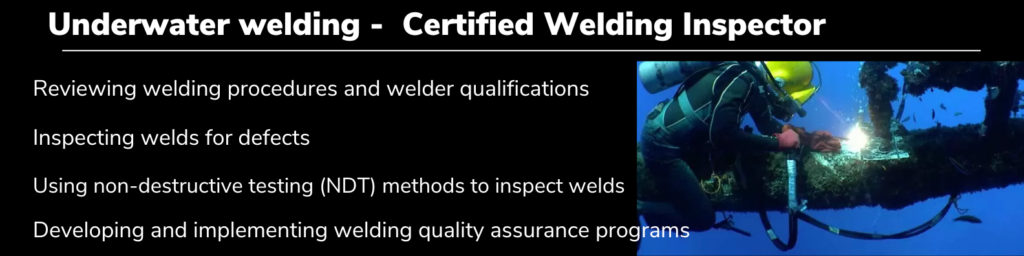
- Reviewing welding procedures and welder qualifications: Underwater welding inspectors must ensure that the welding procedures and welder qualifications meet all applicable codes and standards. This includes reviewing the welding procedures for accuracy and completeness, and ensuring that the welders have the necessary training and experience.
- Inspecting welds for defects: Underwater welding inspectors must inspect welds for defects, such as cracks, porosity, and slag inclusions. They use a variety of non-destructive testing (NDT) methods to inspect welds, such as visual inspection, ultrasonic testing, and magnetic particle testing.
- Using non-destructive testing (NDT) methods to inspect welds: Underwater welding inspectors must use NDT methods to inspect welds for defects. This includes ultrasonic testing, magnetic particle testing, and dye penetrant testing.
- Preparing and issuing welding inspection reports: Underwater welding inspectors must prepare and issue welding inspection reports. These reports document the findings of the inspection, and any recommendations for corrective action.
- Training welders and other personnel on welding inspection: Underwater welding inspectors may be responsible for training welders and other personnel on welding inspection. This includes training on the use of NDT methods, and the identification of welding defects.
- Developing and implementing welding quality assurance programs: Underwater welding inspectors may be responsible for developing and implementing welding quality assurance programs. These programs help to ensure that welded joints meet all applicable codes and standards.
Underwater welding is a complex and challenging process, and underwater welding inspectors play an important role in ensuring the quality and safety of underwater welds. They must have a strong understanding of welding principles and practices, as well as the ability to use NDT methods to inspect welds. They must also be able to work independently and as part of a team, and be able to communicate effectively with engineers, welders, and other stakeholders.
In addition to the above, underwater welding inspectors may also have the following responsibilities:
- Planning and coordinating underwater welding projects: Underwater welding inspectors may be responsible for planning and coordinating underwater welding projects. This includes identifying the welding requirements, developing the welding procedures, and scheduling the welding work.
- Monitoring the welding environment: Underwater welding inspectors must monitor the welding environment to ensure that it is safe for welding. This includes monitoring the water temperature, the current, and the visibility.
- Overseeing the welding process: Underwater welding inspectors must oversee the welding process to ensure that it is being carried out correctly. This includes ensuring that the welders are using the correct procedures and equipment, and that they are taking the necessary safety precautions.
- Resolving welding problems: Underwater welding inspectors must be able to resolve welding problems. This may involve identifying the cause of the problem, and recommending corrective action.
Underwater welding inspectors play a vital role in ensuring the quality and safety of underwater welds. Their work helps to prevent accidents and protect workers and the public.
Certified Welding Inspectors Salary
The salary range for Certified Welding Inspectors (CWIs) varies depending on the level of experience, the industry, and the location.
- Junior CWI: A junior CWI typically has less than two years of experience and earns an average salary of $50,000 per year.
- Mid-level CWI: A mid-level CWI typically has 2 to 5 years of experience and earns an average salary of $60,000 per year.
- Senior CWI: A senior CWI typically has more than 5 years of experience and earns an average salary of $70,000 per year.
The salary range for CWIs can also vary depending on the industry. For example, CWIs in the oil and gas industry typically earn more than CWIs in other industries.
The salary range for CWIs can also vary depending on the location. For example, CWIs in major cities typically earn more than CWIs in rural areas.
In addition to salary, CWIs may also receive benefits such as health insurance, retirement plans, and paid vacation.
Here are some factors that can affect the salary of a Certified Welding Inspector:
- Experience: The more experience a CWI has, the higher their salary will be.
- Industry: The industry in which a CWI works can also affect their salary. For example, CWIs in the oil and gas industry typically earn more than CWIs in other industries.
- Location: The location in which a CWI works can also affect their salary. For example, CWIs in major cities typically earn more than CWIs in rural areas.
- Certifications: CWIs who have additional certifications may earn more than CWIs who do not have any certifications.
- Skills: CWIs who have specialized skills, such as the ability to use certain welding inspection equipment, may earn more than CWIs who do not have these skills.
If you are interested in becoming a Certified Welding Inspector, you should start by gaining experience in welding. You can do this by working as a welder or by volunteering your time to weld projects. Once you have some experience, you can take the CWI certification exam. The exam is offered by the American Welding Society (AWS) and the Certification Scheme for Welding Inspection Personnel (CSWIP).
Once you are certified, you can start looking for jobs as a CWI. You can find jobs by searching online job boards or by networking with other CWIs.
Current Openings of Certified Welding Inspectors
- Zekelman Industries is hiring a CWI for their facility in Chandler, Arizona. The job pays $70,000–$75,000 per year and requires at least ten years of experience in welding and managing / leading.
- Patriot Engineering and Environmental, Inc. is hiring a CWI for their facility in Indianapolis, Indiana. The job pays $30–40 per hour and requires a high school diploma or equivalent, at least two years of welding experience, and a CWI certification
- United Technical is hiring Level II/III NDT Inspectors for their facility in Whitmore Lake, Michigan. The job pays an estimated $45.4K – $57.4K per year and requires a CWI certification and experience with NDT methods.
- Certified Welding Inspector – Integrated Piping is hiring a CWI for their facility in Lake Charles, Louisiana. The job pays $60–$70 per hour and requires at least five years of experience in welding and piping inspection.
- L3 Inspection Services, LLC, is hiring a CWI for their facility in Phoenix, Arizona. The job pays $60 per hour and requires at least five years of experience in welding and inspection.
- Larsen & Toubro is hiring a CWI for their facility in Mumbai, Maharashtra. The job pays INR 800,000–1,000,000 per year and requires at least five years of experience in welding and inspection.
- Bharat Heavy Electricals Limited is hiring a CWI for their facility in Hyderabad, Telangana. The job pays INR 700,000–800,000 per year and requires at least three years of experience in welding and inspection.
- Hindustan Aeronautics Limited is hiring a CWI for their facility in Bangalore, Karnataka. The job pays INR 600,000 – 700,000 per year and requires at least two years of experience in welding and inspection.
- Gujarat Heavy Engineering Corporation is hiring a CWI for their facility in Surat, Gujarat. The job pays INR 500,000–600,000 per year and requires at least one year of experience in welding and inspection.
- Shriram EPC Limited is hiring a CWI for their facility in Chennai, Tamil Nadu. The job pays INR 400,000–500,000 per year and requires at least six months of experience in welding and inspection.
Online Courses of Certified Welding Inspectors
Welding Processes
Course Provider: Indian Institute of Technology, Madras
- Free Online Course
- English
- Paid Certificate Available
- 12 weeks long
Welding Metallurgy
Course Provider: Indian Institute of Technology, Roorkee
- Free Online Course
- English
- Paid Certificate Available
- 12 weeks long
Analysis and Modeling of Welding
Course Provider: Indian Institute of Technology, Madras
- Free Online Course
- English
- 8 weeks long, 2-3 hours a week
Fundamental of Welding Science and Technology
Course Provider: Indian Institute of Technology, Guwahati
- Free Online Course
- English
- Paid Certificate Available
- 8 weeks long
Welding Application Technology
Course Provider: Indian Institute of Technology, Guwahati
- Free Online Course
- English
- Paid Certificate Available
- 8 weeks long
Welding Of Advanced High Strength Steels For Automotive Applications
Course Provider: Indian Institute of Technology Madras
- Free Online Course
- English
- Paid Certificate Available
- 4 weeks long
Conclusion
Certified Welding Inspectors (CWIs) stand as sentinels of integrity, safety, and quality in the realm of welding. Throughout this exploration of their role, it becomes evident that CWIs are not mere observers; they are the bedrock of industries, the architects of safety, and the guardians of standards.
In a world where welds uphold structures, where precision ensures longevity, and where safety is paramount, CWIs emerge as essential figures. Their trained eyes scrutinize welds, their expertise identifies potential defects, and their unwavering commitment ensures compliance with codes and regulations.
As the silent force behind the scenes, CWIs prevent costly rework, reduce downtime, and elevate the outcomes of projects. They foster a culture of quality assurance and safety, enriching the environments we inhabit and the structures we rely on.
In the dynamic landscape of welding, CWIs are not just inspectors; they are drivers of progress. Their dedication to lifelong learning, their adaptability to emerging technologies, and their role in shaping a safer, more reliable future cannot be understated.
FAQ
What are the qualifications of a certified welding inspector?
The qualifications for a Certified Welding Inspector (CWI) vary depending on the organization that offers the certification. However, all of the certifications require a certain level of education, experience, and knowledge in welding inspection.
Here are the general qualifications for becoming a CWI:
Education: A high school diploma or equivalent is required. Some organizations may also require an associate’s or bachelor’s degree in welding engineering or a related field.
Experience: A minimum of two years of welding experience is required. Some organizations may also require experience in a specific industry, such as the oil and gas industry or the construction industry.
Knowledge: A thorough understanding of welding principles and practices is required. CWIs must also be able to read and interpret technical drawings, and use non-destructive testing (NDT) methods to inspect welds.
Examination: All CWI candidates must pass a written and practical exam. The written exam covers welding principles and practices, NDT methods, and welding inspection. The practical exam requires candidates to inspect welds and prepare inspection reports.
In addition to the above, some organizations may also require CWIs to have certain skills, such as:
*Excellent communication skills
*The ability to work independently and as part of a team
*The ability to use welding inspection equipment
If you are interested in becoming a CWI, I recommend that you research the different certification programs available and choose one that is right for you. You should also gain as much welding experience as possible before you take the certification exam.
How much does it cost to get CWI certified?
The American Welding Society (AWS) offers the CWI certification. The cost of the AWS CWI exam is $1,070 for AWS members and $1,325 for non-members. The exam is offered at testing centers around the world.
The Certification Scheme for Welding Inspection Personnel (CSWIP) also offers the CWI certification. The cost of the CSWIP CWI exam is £630 for UK members and £780 for non-members. The exam is offered at testing centers in the UK and Ireland.
In addition to the exam fee, there are other costs associated with becoming a CWI, such as:
The cost of study materials
The cost of taking welding classes or workshops
The cost of travel to the testing center
The total cost of becoming a CWI can range from a few hundred dollars to several thousand dollars.
If you are interested in becoming a CWI, I recommend that you research the different certification programs available and choose one that is right for you. You should also factor in the cost of the certification when making your decision.
Here are some other costs that may be incurred when becoming a CWI:
Membership fees: Some organizations require CWI candidates to be members of the organization in order to take the certification exam.
Continuing education: CWI candidates are required to complete a certain amount of continuing education credits every year in order to maintain their certification.
Job search expenses: CWI candidates may incur expenses related to job searching, such as travel expenses and the cost of resumes and cover letters.
The total cost of becoming a CWI can vary depending on the individual’s circumstances. However, by carefully planning and budgeting, it is possible to minimize the costs associated with becoming a CWI.
What is Cswip 3.1 welding inspector?
The American Welding Society (AWS) offers the CWI certification. The cost of the AWS CWI exam is $1,070 for AWS members and $1,325 for non-members. The exam is offered at testing centers around the world.
The Certification Scheme for Welding Inspection Personnel (CSWIP) also offers the CWI certification. The cost of the CSWIP CWI exam is £630 for UK members and £780 for non-members. The exam is offered at testing centers in the UK and Ireland.
In addition to the exam fee, there are other costs associated with becoming a CWI, such as:
The cost of study materials
The cost of taking welding classes or workshops
The cost of travel to the testing center
The total cost of becoming a CWI can range from a few hundred dollars to several thousand dollars.
If you are interested in becoming a CWI, I recommend that you research the different certification programs available and choose one that is right for you. You should also factor in the cost of the certification when making your decision.
What is the salary of Level 3 CSwip?
The salary range for Level 3 CSWIPs can be as low as ₹15 lakhs per year and as high as ₹35 lakhs per year. The salary range is affected by the following factors:
Experience: The more experience a Level 3 CSWIP has, the higher their salary will be.
Industry: The industry in which a Level 3 CSWIP works can also affect their salary. For example, Level 3 CSWIPs in the oil and gas industry typically earn more than Level 3 CSWIPs in other industries.
Location: The location in which a Level 3 CSWIP works can also affect their salary. For example, Level 3 CSWIPs in major cities typically earn more than Level 3 CSWIPs in rural areas.
Certifications: Level 3 CSWIPs who have additional certifications may earn more than Level 3 CSWIPs who do not have any certifications.
Skills: Level 3 CSWIPs who have specialized skills, such as the ability to use certain welding inspection equipment, may earn more than Level 3 CSWIPs who do not have these skills.
If you are interested in becoming a Level 3 CSWIP, you should start by gaining experience in welding inspection. You can do this by working as a welding inspector or by volunteering your time to inspect welds. Once you have some experience, you can take the Level 3 CSWIP certification exam. The exam is offered by the Certification Scheme for Welding Inspection Personnel (CSWIP).
Once you are certified, you can start looking for jobs as a Level 3 CSWIP. You can find jobs by searching online job boards or by networking with other Level 3 CSWIPs.
What is the cost of Cswip 3.1 in India?
Here are some of the training providers in India that offer CSWIP 3.1 training:
* Imech Institute
* BIT Inspection Technology
* Welding Quality Concepts
* TWI India
* Welding Training Institute
When choosing a training provider, it is important to compare the costs, the curriculum, and the reputation of the provider. You should also make sure that the provider is accredited by the Certification Scheme for Welding Inspection Personnel (CSWIP).